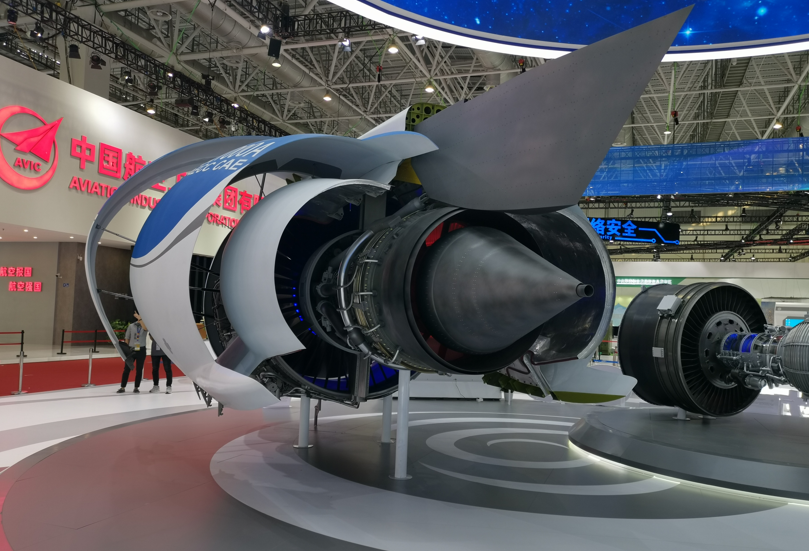
中国航空发动机集团简介、直属单位与主营业务
2022年04年24日
CompositesWorld 2025-01-27
多功能机身演示器 (MFFD) 是 Clean Sky 2(现为Clean Aviation)项目的一部分,历时约 10 年,生产出了最大的飞机结构——8 × 4 米直径的机身部分,完全由热塑性复合材料 (TPC) 制成。此外,其众多组件被焊接在一起,旨在展示“无尘组装”,这可以消除在复合材料主结构中钻孔和安装紧固件的多步骤工艺链、劳动力、时间、成本和重量。
多年来, CW通过多篇文章和新闻稿报道了该项目。正如CW 2023 年的文章“制造 MFFD 热塑性复合材料机身”中所解释的那样,MFFD 下壳体和上壳体的组装始于左侧 [LH] 侧对接纵向机身接头。这项工作已在2024 年 3 月宣布的BUSTI 项目中完成,其中 8 米长的连接是使用一种名为 CONTIjoin 的基于 CO2 激光的连续连接技术实现的,该技术由德国德累斯顿弗劳恩霍夫材料与光束技术研究所 (IWS) 开发。
完成 CONTIjoin 之后,完成 MFFD 组装的最后步骤包括使用连续超声波焊接焊接右侧 (RH) 搭接接头。最后,对上半部和下半部的机身框架耦合器进行电阻焊接,以实现 LH 和 RH 接头的连续结构。
正如我在 2020 年的博客“验证 MFFD 的 LMPAEK 焊接”中所解释的那样,MFFD 各个组装步骤中使用的焊接技术很早就已确定。“MFFD 将展示许多技术方法,”空中客车运营有限公司(德国不来梅)机身 R&T 典型机身负责人兼 MFFD 项目负责人 Ralf Herrmann 指出,“因此它与制造实际机身不同,而是被设计为展示和完善技术的工具。”
机身框架的 RH 搭接和焊接是在 MultiFAL(2019-2023 年)和 WELDER(2021-2023 年)项目中由主要合作伙伴CT 工程集团(西班牙马德里)、 AIMEN 技术中心 (西班牙奥波里尼奥)和Aitiip 技术中心(西班牙萨拉戈萨)在超声波设备供应商Dukane(美国伊利诺伊州圣查尔斯)通过其位于捷克共和国布拉格的子公司和生产自动化专家FFT (德国富尔达)的帮助下完成的。本文将介绍 MFFD 的最终组装步骤及其成功所需的技术。
对于这两个项目,空中客车公司是清洁天空项目经理,而 CT 工程集团是联合体协调员。MultiFAL 还由位于 CFK NORD 研究中心(德国施塔德)的弗劳恩霍夫制造技术与先进材料研究所(IFAM) 管理,MFFD 的最终组装将在此进行。
CT Engineering 研发项目经理 José Maria Rodríguez Valenzuela 表示:“我们的任务是开发和提供连接机身上半部和下半部的自动化系统。”他解释说,MultiFAL 的目的是重复使用 Fraunhofer IFAM 原型装配站,集成硬件和控制系统以进行必要的定位和焊接操作。该联盟还包括开发在线监控系统的 FFT 和 AIMEN。软件供应商Dassault Systèmes (法国韦利济-维拉库布莱)的 3DExperience 平台使团队和利益相关者之间的协作能够支持 CAD/CAM、装配和模拟。
“首要目标是根据要求设计并向装配设施项目经理提出一些概念,”Valenzuela 说道。“IFAM 和空客随后选择了首选概念,我们根据对焊接过程中应力和所有工艺负载的分析,设计了将安装机身两半的设施 [装配平台和系统]。然后,我们着手制造该设施及其定位系统。首先,我们在设计中准备了装配过程的数字模型。结果不仅是设施的钢结构,还有 FFT 的焊接末端执行器控制系统(稍后将在 WELDER 项目中集成),以及所有操作机制和所需的公差。我们不仅要考虑机身外壳的组装,还要考虑操作员的活动,包括如何提供检修平台以及管理各种放置、焊接和测量活动所需的机制和软件。
“在我们开发自动装配设备的设计的同时,空客及其合作伙伴也在设计机身上下外壳,”Valenzuela 继续说道。“两年后,我们启动了 WELDER 项目。”WELDER 的主要目标是设计、开发和部署两种基于机器人的模块化灵活焊接解决方案,包括工装和辅助设备,以完成 8 米长的 RH 机身接头,并随后连接 RH 和 LH 机身接缝上的上下机身框架。AIMEN 与超声波设备供应商 Dukane 合作,开发了用于机身接头连续超声波焊接的末端执行器。同时,Aitiip 设计并制造了电阻焊接末端执行器以及连接机身框架所需的 TPC 耦合器。“这些部件具有不同的几何形状,使用热成型压机制成,”Valenzuela 说道。“它们经过修整后,与焊接工具一起运往德国,安装在 MultiFAL 装配站。然后,我们将超声波焊接末端执行器安装在外部线性轴上,将电阻焊头安装在机身内部的线性轴上。”
“我们领导了焊接工艺的开发,包括系统设置和大量试样测试,以确定两种工艺的工艺窗口和最佳参数,”AIMEN 先进复合材料技术负责人 Elena Rodriguez 博士说道。“我们还与 Aitiip 合作开发电阻焊接中的加热元件,并提供在线监控系统来捕获两种焊接操作的数据。”
在超声波焊接中,超声波发生器通过 TPC 层压板发送振动,在焊接界面产生热量,但这通常需要在焊接的两个部件之间放置能量导向器(一层非增强树脂,传统上带有三角形突起,有助于集中能量)。AIMEN 复合材料焊接团队负责人 Massimiliano Russello 博士指出,尽管超声波焊接在点焊方面已经发展成熟,但在连续焊接方面还不太成熟。他指出,在为最终的 MFFD 机身接头开发连续超声波焊接工艺方面面临许多挑战,包括为如此长的焊缝(8 米)开发连续工艺以及如何实现搭接接头设计。
“我们最终决定分三步完成,”罗德里格斯说。这三个步骤,或者说焊接工具的三次操作,使得上壳中的阶梯式层压板与下壳中的阶梯式层压板连接在一起,但每个步骤的工艺参数都不同。“设计一种可以焊接所有三个步骤的工具,同时确保零件之间的接触压力和稳定性,这是一个挑战。此外,我们实验室规模的连续焊接机长度不足 1 米,因此我们必须对工艺进行参数化,以扩大规模。”
“对于 MFFD 中使用的高温 TPC 材料(主要是来自威格斯(英国克利夫利斯)的东丽先进复合材料公司(TAC,荷兰奈弗达尔)的碳纤维增强 LMPAEK 聚合物单向(UD)带),在如此大而厚的部件中以连续模式使用尤其具有挑战性,”Russello 补充道。“为了以连续快速的方式将上壳焊接到下壳上,我们必须只从一侧焊接,并使用三种不同厚度的焊道,厚度最高可达 3.5 毫米。厚度越大,焊接难度越大。”这是因为很难对非常厚的部件进行振动,并将振动传递到焊接界面。
焊接末端执行器。Russello解释说,除了超声波头之外,右侧的滚轮可确保部件接触,左侧的冷却或固结块可在加热固结后对部件施加压力。“该块还吸收来自焊接界面的热量。”在最终的超声波焊接头中,铝冷却块被铜块取代,以提高导电性和吸热性,从而实现更高的表面质量。
参数和工艺缩放。有许多参数会影响焊接过程,包括压力、超声波振幅、时间和冷却。此外,部件的铺层、导电性和厚度也很重要。这些都会影响温度分布、加热行为和能量耗散——这是一种复杂、相互关联的机制,在焊接过程中不断发展,Russello 说。
“我们从实验室规模开始,使用非常简单的设置,然后逐渐增加复杂性,最终得到集成到 MultiFAL 设施中的焊接头,”他继续说道。“从实验室规模开始,我们安装了监控系统,包括热像仪和温度传感器,并对所有不同参数进行了长期研究,包括数值模型,以了解对温度发展和焊接质量的影响,以及我们如何使用监控系统来确保质量。
“然后我们转向中等规模,焊接了 2 米长的条带,以验证并与实验室规模的条带进行比较,”Russello 说道。“我们校准了 2 米面板的参数和性能,焊接效果非常好,并对其进行了机械和无损检测测试。使用监控系统、数值模型和模拟,我们可以将其与全尺寸演示器相关联。我们能够证明中等规模的参数也适用于整个机身部分,这是一个非常关键的结果。”
温度控制。下一个挑战是设计一个精心设计的焊头温度控制。Russello 解释说,在连续焊接过程中,“焊接时间取决于移动焊头的速度。”请注意,这包括冷却,冷却必须在精确的窗口内进行,以在 LMPAEK 聚合物中形成必要的结晶,从而实现机械强度。“但移动过程中也会主动冷却,这意味着冷却速度取决于移动焊头的方式,”Russello 指出。“因此,如果移动速度更快,冷却部件的时间就会减少。要么优化参数,要么重新设计冷却系统,因为焊接需要这种速度。这一切都是相互关联的。”
对于 MFFD,AIMEN 团队从机身外侧进行焊接。但在内部,有金属固定块,以防止在施加压力时移动,这也会从焊接的部件中吸收热量。这又回到了三个焊接步骤或道次,以及每个步骤所需的不同参数。“当焊接的背面层压板非常薄时,”Russello 说,“热量很容易进入固定块。但在最顶部较厚的台阶上,将焊接热量传递到固定块需要更长的时间,这意味着如果你没有提供足够的冷却,焊缝就会在这个区域脱层。”
“通过简单分析冷却块后的温度,”他继续说道,“我们能够了解焊接后部件的表现。当温度低于 145°C 时,我们无法实现部件的固结。但当温度超过 150°C 时,我们遇到了一些分层。通过监测固结单元后的温度(在表面,而不是在焊接界面)并根据工艺参数进行校准,我们能够确保实现充分冷却并避免焊接后分层。”
一次成功。 “与我们研究过的其他技术相比,超声波焊接非常高效、快速,”Russello 说道,“但如果没有之前的历史信息,很难一次性完成机身焊接,而且一次成功。”
Valenzuela 表示同意,并强调道:“我们每一步只有一次焊接机会,尽管 AIMEN 进行了许多测试来确定参数,但当团队开始焊接 MFFD 时,上壳中的层压板并不像他们预期的那样,与他们测试的有所不同。”因此,团队不得不调整一些参数,但他们的校准和监控系统有所帮助,最终他们能够达到所需的焊接质量。Valenzuela 说,这真的很重要。“这是该项目的主要目标。”
超声波焊接完成后,机身上下壳体连接在一起,WELDER团队使用电阻焊接连接机身框架。Aitiip负责制造连接结构框架的TPC耦合器,然后将其电阻焊接在机身内部的RH和LH侧。
自动化工具。Aitiip机器人技术负责人 Iván Monzón 解释说,第一个挑战是如何将耦合器定位到机身框架上。“最初,我们设想使用机器人来完成这项工作,这样可以提供更大的灵活性。但机身内部的空间非常有限。因此,我们需要创建一种专用工具来管理组件并将它们放在正确的位置进行焊接。”
该团队设计了一种安装在推车上的工具,该推车沿着机身内的直线轨道移动。它是自动化的,使用控制软件将耦合器放置在需要焊接的位置。该工具重 15 公斤,尺寸为 600 × 450 × 250 毫米,加上推车,总尺寸为 1,200 × 450 × 800 毫米,重 50 公斤。“这很轻,”Monzón 解释说,“考虑到该设备在焊接过程中的作用类似于压力机,需要材料刚度。它还通过两个不同的头执行电阻焊接动作,用于焊接上部和下部位置以及四种类型的耦合器几何形状。”
焊接耦合器。焊接是通过将电流通过耦合器中的两个接触点来实现的。这熔化了耦合器和框架中的热塑性基质,同时施加压力以通过旋转接头上的气动缸将零件熔合在一起。使用压力点的称重传感器监测压力。“这个操作是在下部和上部区域同时进行的,”Monzón 说,“完美地连接了整个结构。每个 MFFD 框架都完成了这一操作。”
“得益于弯曲导轨系统,耦合器焊接工具可以适应所有曲率,”他补充道。“这些导轨跨越了被连接的框架之间的距离,并确保耦合器上的导电元件接触两个框架,以便进行焊接。该系统还能够适应从耦合器到框架的理论位置到安装和定位误差高达 30 毫米。”
WELDER 的项目经理兼空客集成工作包负责人 Piet Wölcken 解释道:“由于框架联轴器是最后的主要接头,我们始终意识到几何不一致性和基本公差都会在这个组装步骤中累积。因此,我们选择了具有合理容错能力的电阻焊接技术来进行框架联轴器集成,即使这意味着在安装过程中需要额外的自由度。”
他指出,该工具也是可逆的。“我们可以将其拆开,然后以相反的方向将其安装在飞机的另一侧,其工作原理相同。”事实上,这种方法使团队能够在超声波焊接的右侧连接 14 个框架,拆开工具,重新安装,然后在之前激光焊接的左侧连接 12 个框架,由于门切口,左侧的框架较少。
“我们采用新技术制造耦合器的方式也很重要,”Monzón 说道。“我们使用了冲压工艺,在注塑机中设置加热模具,可以非常快速地生产出零件。”他解释说,注塑成型是 Aitiip 的核心专长,“因此我们利用这些知识和机器来制造这些耦合器。我们从扁平碳纤维增强热塑性复合材料板开始,这些复合材料板由 UD 胶带制成,具有高结构性能。将它们切割成形状并放入模具中。”然后使用放置在注塑机内的陶瓷灯阵列将它们预热到 360°C 至 400°C 之间。一旦达到预热温度,灯就会通过液压驱动从注塑机中移出,从而使注塑机关闭。“整个过程都在控制范围内,并在不到 10 秒的时间内完成,因此材料不会冷却,”他补充道。
三个部件在同一模具中压制成型,经过 4 分钟的灯光加热 + 10 秒的闭合 + 3 分钟的冷却结晶 + 10 秒的打开脱模,整个循环时间不到 8 分钟。Monzón 说道,这不仅加快了生产速度,“而且还有助于在成型过程中保持弯曲力的对称性,从而使该工艺可行。正如您在部件中看到的,曲率并不只有一种——有些区域有两三种不同的曲率,因此几何形状相当复杂。不可能不产生皱纹或扭曲地弯曲板材——这些曲率中会存在材料缺失或材料过剩的区域。因此,我们在一个半模具的中心使用弹簧来解决这个问题,这样能够在整个过程中保持部件的张力,从而防止起皱。”
这些部件在模具中冷却至低于玻璃化转变温度(147°C)然后取出。六轴机器人铣床用于提取和修整这三个部件以达到最终公差。Monzón 表示,与传统的热固性复合材料部件相比,这一工艺将周期时间缩短了 50% 以上,以最少的制造设备投资使产量翻了一番。
Wölcken 表示,MFFD 封盖的主要焊接操作已精确完成,并有足够的时间在 2023 年 7 月将其运送到汉堡 ZAL 应用航空研究中心有限公司之前安装最终的局部部件。 “这一里程碑的实现完全归功于各个 MFFD 项目联盟人员的极度奉献和协作精神,以及 WELDER 和 MultiFAL 联盟与弗劳恩霍夫 IFAM 和空客的出色工作。”
在 ZAL,MFFD 进入下一阶段,成为 Clean Sky 的 NextGen 客舱和货物概念的演示者,该概念标准化了机身和定制客舱及系统组件之间的接口。这包括一个新的“皇冠模块”,由天花板区域和“帽架”以及电气、空调和氧气供应组件和许多机械固定装置组成。MFFD 皇冠模块预先组装并安装到机身中,只需一个连接步骤,它由帝人碳素欧洲公司(德国伍珀塔尔)的 TPUD HT CF-PPS 热塑性切割胶带与Spiral RTC(荷兰恩斯赫德)的再生 Spiral 轻质 PPS CF40 复合材料制成的超轻棒构成。这些可调节长度的棒是如何在 TPC 机身系统中重新利用 TPC 零件生产废料的一个很好的例子。
“MFFD 仍在评估中,它是众多后续项目和计划的进一步工作和灵感来源,”Wölcken 说道。这些项目包括 FASTER-H2、PENELOPE(欧盟地平线 2020 项目)、ZEUS 和 HESTIA,后者是德国资助的 LuFo 航空研究计划的后半部分。“MFFD 是一个很好的例子,它使用一个主要的先锋项目来展示大量单独的 CFRTP 技术(在某些情况下甚至是技术变体)的潜力。随后,其中一些单独的技术被选中进行进一步的、高度驱动的开发。例如,LuFo HESTIA 项目包含用于高速生产大型复杂机身框架结构的关键开发模块等。”
Monzón 表示:“WELDER 项目展示了创新制造技术如何增强航空航天业的结构完整性和可持续性。通过利用热塑性复合材料并缩短循环时间,该团队实现了显著的效率提升,同时最大限度地减少了资源消耗。此外,这种方法使复合材料的生产更易于获取且更具成本效益,从而使复合材料的使用更加大众化,同时也促进了复合材料的可回收性和可重复使用性。这不仅提高了制造产量,而且符合该行业对环保和循环生产系统的目标。”
2022年04年24日
2022年04年20日
2019年12年07日
2019年12年13日
2023年03年18日
2019年12年11日
2019年12年12日
2019年10年05日
2022年04年12日
2022年05年03日
评论 (0)