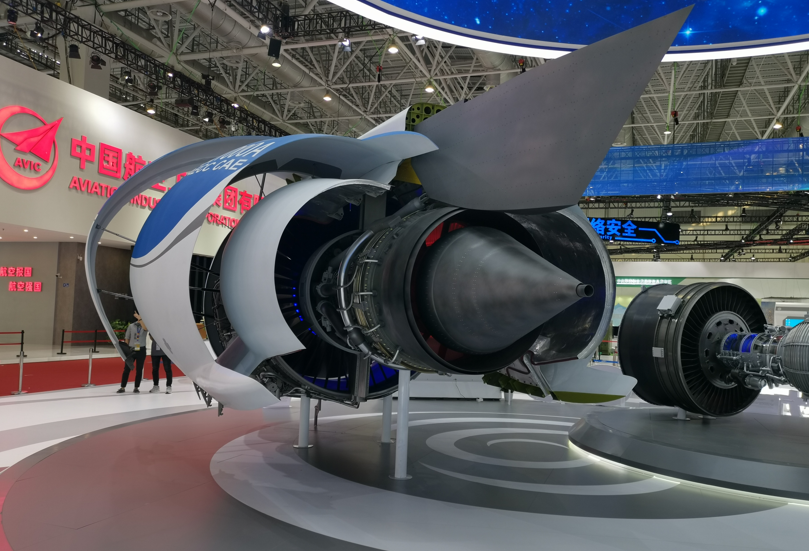
中国航空发动机集团简介、直属单位与主营业务
2022年04年24日
中国建材报 2023-07-12
为响应《国家中长期科技发展规划纲要(2006—2020年)》《建材工业“十三五”发展规划(2016—2021年)》《产业结构调整指导目录》等文件号召,耀皮玻璃集团历时十余年进行“卡脖子”技术——航天航空领域特种玻璃制造技术研发,攻克大飞机风挡玻璃原片设计、生产、测试技术,成为全球第三家大飞机航空玻璃原片供应商。飞机风挡玻璃有哪些特殊性能要求?生产过程中取得了哪些技术突破?本报对耀皮玻璃集团常熟生产基地总经理李志进进行了专访。
耀皮航空玻璃第一片航空玻璃下线 耀皮玻璃集团/供图
问:电影《中国机长》中,机舱风挡玻璃破裂、副机长飞出去的画面记忆犹新。与汽车用风挡玻璃相比,飞机风挡玻璃有哪些特殊性能要求?结构有何不同?
李志进:耀皮玻璃研发的是航空玻璃原片,因此我们只能谈航空玻璃原片的主要特点。相比汽车用风挡玻璃,安全对于飞机风挡玻璃来说更为关键。它不但要为驾驶员提供良好的视觉效果,还要承受高速飞行时的风压、冰雹和飞鸟撞击、沙尘的摩擦、急速温差、室内外温差和压差等一系列复杂环境要求,这也赋予了飞机风挡玻璃的特殊性能要求。具体包括:
玻璃强度高:航空玻璃需要承受高风压和冰雹等恶劣天气的影响,玻璃强度对飞行安全至关重要。航空玻璃原片需通过落球试验验证,在未钢化的情况下其抗冲击强度能达到普通机车玻璃钢化后的水平(较钢化前提高3~5倍)。
易于化学钢化:航空玻璃在飞机起降过程中要经受风沙的反复剧烈摩擦,因此表面耐磨强度是影响玻璃寿命的重要指标,而化学钢化可以显著提高玻璃表面的压应力,大大改善玻璃的耐磨性能。
光学性能好:航空玻璃需要有通透的视线,并且不能影响飞行员的视觉效果,不能有任何光学畸变。通过原料和工艺技术的创新,不但玻璃的透光率要达到超白玻璃水平,而且玻璃还要具有优异的紫外线阻挡能力,能显著降低高空飞行过程中太阳光的强烈辐照。
缺陷密度低:玻璃缺陷会造成玻璃应力局部集中,显著降低玻璃的强度。航空玻璃利用先进生产工艺,在克服玻璃黏度高、均化难度大等不利因素下,使得玻璃缺陷数量远远低于高档浮法玻璃,成品玻璃使用50倍放大镜都检查不到相关缺陷,保证了玻璃的使用强度。
耀皮航空玻璃原片样片 耀皮玻璃集团/供图
问:飞机风挡玻璃可谓是集玻璃行业所有高精尖技术为一体,耀皮玻璃集团在航空风挡玻璃原片制造方面进行了哪些技术突破?在实现量产过程中对生产线做了哪些调整?
李志进:航空玻璃的制作工艺复杂,几乎包含了玻璃加工行业的所有高精尖技术,航空玻璃制造也被称为“玻璃加工技术之花”。耀皮玻璃集团形成了系统、成熟、可复制的航空玻璃原片生产技术,主要表现在:开发出适配于大飞机风挡玻璃性能要求的铝硅系玻璃组分,满足了航空玻璃性能和化学钢化的要求;开发出全氧电辅助燃烧技术,突破了无钙玻璃熔化和均化澄清困难的工艺难题;开发出纳米增强除油膜辅助澄清技术,解决了高温玻璃液表面类油状的薄膜层对气泡排出的阻挡,消除影响澄清效果的不利因素;开发出熔窑高温气幕隔离飞料技术,突破了超细配合料高温飞散、不均匀挥发这些影响产品质量的难题;研发出成套航空玻璃原片成套生产技术,包括全新的生产线设计、与其配套的生产工艺技术、原料及最终玻璃产品评价标准和检测方法等,都具有完全知识产权和可重复性。
问:耀皮玻璃集团为什么愿意花十几年时间攻克飞机风挡玻璃技术的生产难题?这对于我国玻璃行业有哪些重要意义?
李志进:航空玻璃原片作为民用大飞机风挡玻璃的关键原材料,关系到飞行员和整架飞机的安全,它在结构强度、光学性能、微观质量等性能方面要求极高,规模化、工业化制造难度极大。我国在民用航空玻璃原片上的研发和生产长期以来都是空白,航空玻璃原片已经成为制约我国民用航空玻璃发展的“卡脖子”关键材料。
耀皮玻璃集团是国内首家引进国外先进浮法生产技术的企业,距今已有40年的历史,在玻璃生产和研发上积累了大量经验。作为国内浮法玻璃技术的引领者,耀皮玻璃有责任和义务去攻克“卡脖子”难题。
项目成功后,耀皮玻璃集团成为继美国PPG、法国圣戈班之后的全球第三家大飞机航空玻璃原片供应商。这是我国浮法玻璃技术一次重大突破,是对我国航空产业的重大贡献。该项目形成了具有国内自主知识产权、系统、成熟、可复制的大飞机航空玻璃原片生产技术,打破国外在该关键核心材料上的垄断,助推我国大飞机工程产业的快速发展。
问:从技术攻关到将玻璃真正用在大飞机的过程中,有哪些令人难忘的瞬间?
李志进:由于该项目是一个完整、系统性的产品研发,涉及的内容十分复杂。实验室是研发的第一步,根据民航客机对玻璃原片的质量要求,例如强度、化学钢化、光性能、耐候性等具体指标,制定玻璃组分,根据组分选择可用的原料,在这过程中还要充分考虑对工业化生产的影响。在实验室里经过称量、混合、熔化、成型、研磨、抛光后,测试玻璃的上述各项性能。我们前后试验了总共不下30种不同元素的各种排列组合,最终选择了数种主要元素,还有几种微量元素。不同元素对玻璃性能的影响不同,即使元素种类已经确定下来了,各种元素百分比含量的不同又会对玻璃性能产生影响。因此,整个试验过程要在实验室中反复进行,前后试验了不下千次。通过不断优化和调整,才最终把玻璃组分确定下来。
工业化设计同样是一个十分复杂的过程,需要通盘考虑玻璃成分、原料特性、工艺特点等,生产线的研发是一个庞大的系统工程,仅尺寸设计就涉及几百个参数。基于耀皮多年来对浮法玻璃的持续研发和经验积累,同时经过大量的物理和数学模拟,根据航空玻璃的特性,确定了最佳的技术路线和生产线各具体尺寸。同时,针对个别信心不足或没有十足把握的问题,还要制定备用方案。因为浮法生产是连续、长年不能停的,如果有问题,必须有备选方案及时跟上。就算一条50吨的微型生产线,如果因为某种原因停窑,每天的损失就是几十万元。如果玻璃料方不对,就算及时使用了正确的料方,也要大约10天左右才能取到玻璃,这个损失是非常大的。另外,研发过程中还要考虑玻璃生产出来以后怎么评价,采用哪些质量管控措施、检测方法、检测手段、质量评估项目、评估标准和评估方法等,都需要配套研发。这是一个系统性、全方位的,从实验室到商品的全过程研发。
可以说,细致入微、精益求精贯穿航空玻璃研发的整个过程,对玻璃性能和浮法技术的综合熟练掌握在整个系统研发中发挥了关键作用。这得益于耀皮玻璃在浮法技术和产品研发上多年的不懈耕耘,形成了深厚的技术积淀并培养了一大批专业技术人才。
2022年04年24日
2019年12年07日
2022年04年20日
2019年12年13日
2023年03年18日
2019年12年11日
2019年10年05日
2019年12年12日
2022年04年12日
2022年05年03日
评论 (0)