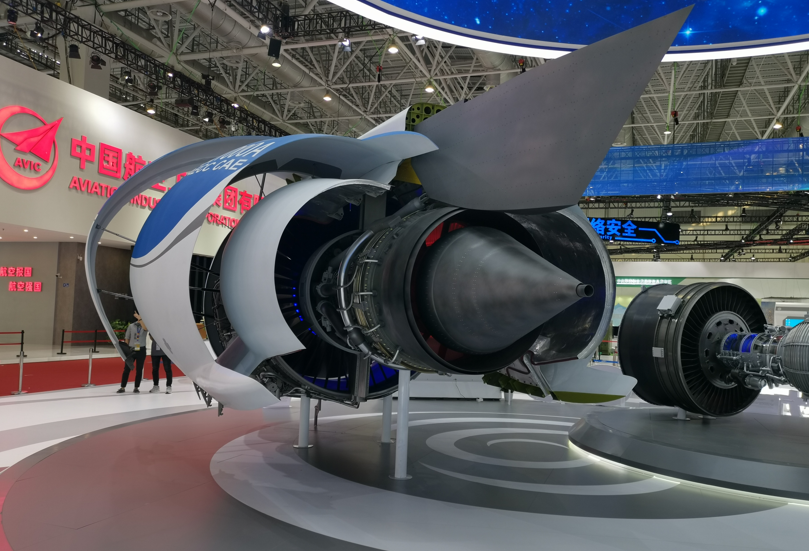
中国航空发动机集团简介、直属单位与主营业务
2022年04年24日
CompositesWorld 2025-05-05
Clean Sky 2 外翼盒 (OWB) 全尺寸演示器的测试取得了里程碑式的进展,达到了技术就绪水平 (TRL) 5,验证了其未来应用的可行性,并为航空航天制造业的进步奠定了基础,从而实现减轻重量和更高效的装配技术。
OWB 演示项目于 2014 年至 2024 年间运行 ,代表了一种区域性飞机机翼结构,旨在验证新兴技术,例如非热压罐液态树脂灌注 (OOA LRI)、热塑性复合材料原位固结、无垫片组装和结构健康监测 (SHM) 传感器系统。该项目由多家航空航天行业领军企业和研究机构共同合作完成,其中包括希腊航空航天工业公司 (HAI)、诺丁汉大学 VADIS 研究中心、那不勒斯大学 (UNINA)、ItalSystem Srl 以及意大利航空航天研究中心 (CIRA) Air Green 2。该项目负责人是 Leonardo。
全尺寸OWB演示器是飞机机翼的结构核心(也是与机身的关键接口),其根部肋条宽度约为9.1米,翼尖肋条宽度约为1.3米,翼尖肋条宽度约为0.7米。它包含多个通过LRI/OOA工艺制造的部件,包括:
正如莱昂纳多公司 Clean Sky 2 REG IADP 项目经理 Vittorio Ascione 所指出的,OWB 演示器的主要目标是全面验证先进的制造工艺和创新的装配方法。
“为了确保某些技术的评估,需要达到飞机上将要使用的全尺寸,”Ascione说道。“因为通过全尺寸测试,你可以发现一些小尺寸演示器无法发现或预见的新问题。在整个过程中使用全尺寸演示器让我们确信一切运行良好,技术评估也真正全面。这是我们首次生产长度超过9米的演示器——这本身就是一项重大成就——这增加了以全尺寸测试这些新技术的可能性。”
然而,开发大型集成复合材料板面临诸多挑战。克服这些挑战的关键技术包括:OOA、LRI、无垫片组装、确定性组装和部件对部件组装:
OOA LRI 流程
该工艺旨在生产大型整体加筋复合材料板,以提高效率并减少环境影响。与传统的基于热压罐的复合材料制造工艺不同,与在热压罐中使用预浸料的传统复合材料工艺相比,使用OOA LRI可以使组件以更少的能量进行“固化”(因为固化过程中无需加压),并且在开始生产之前无需使用大型制冷机来保存复合材料。这种方法可减轻2%的重量,如果应用于在役的OWB,将转化为燃料的节省和排放的减少。
无垫片组装
无垫片装配技术的发展需要扫描、逆向工程和 CAM 软件的无缝集成。
“传统上,翼盒组装需要使用垫片来填补肋条和壁板之间的间隙。这个过程既费时又费钱,“莱昂纳多公司”清洁天空2“项目REG IADP OWB演示负责人Giuseppe Totaro解释说。“我们的新方法利用数字孪生和精密加工来创建无垫片配置。”
无垫片装配基于对公差传递的研究以及“确定性装配方法”(DAA)。这是一种制造和装配方法,可确保零件以最小的调整完成装配,从而减少装配过程中对垫片、返工或手动装配的需求。DAA 依靠精密工程、数字化设计和公差管理,打造出组装时完美对齐的组件。这种方法由 VADIS(偏差感知确定性装配集成系统)项目开发,允许在尽可能的情况下通过增加公差来优化公差,同时降低制造成本。
这一挑战也通过改进自动化软件程序来解决,确保与 Catia 等现有行业工具兼容。利用逆向工程,开发了自动化软件程序来扫描面板表面并确定最终的肋条表面,以实现精确的零件对零件装配——这是一种通过连接两个或多个零件来创建组件的方法,其中零件可以相互接触或相互挤压,并可用于创建新的零件或子组件。
最终的演示器长度超过 9 米,通过减少对垫片的需求并实现一次性完成孔而不是多次完成,成功地证明了这种方法的效率,从而将制造成本降低了 4%。
结构健康监测(SHM)
该项目的一个关键特点是集成了SHM压电传感器和光纤,并将其巧妙地嵌入翼盒中,以监测OWB结构的应力和状态。该项目已成功完成测试,证明了其在检测、定位和跟踪复合材料结构损伤扩展方面的有效性,确保了长期的可靠性和安全性。
“我们与Air Green 2联合体合作,在复杂的翼盒内安装了电子传感器。这项全尺寸安装是为了验证这些技术,考虑到演示机长达9.1米,这一点尤为重要。“莱昂纳多公司的Ascione说道。
这项技术不仅通过实时监控提高了飞机的安全性,而且还通过收集可用于预测未来何时需要维护和维修的数据来帮助进行预测性维护。
经过包括全尺寸静态弯曲试验在内的严格测试,该项目成功验证了这些技术,证实了实验数据与数值模型之间的高度相关性。这项验证对于获得TRL 5级至关重要,证明了这些技术在未来航空航天应用中的可行性。
未来的应用和后续步骤
OWB 演示器的成功为欧洲航空航天制造业的进一步发展铺平了道路:在整个项目过程中开发的流程 - 特别是用于集成纵梁、肋骨和翼梁的全尺寸加固面板的全尺寸 LRI 制造流程 - 不仅适用于支线飞机,也适用于其他尺寸的飞机(无论更大还是更小),这些飞机的生产成本和环境影响要求更具挑战性。
“我们开发的技术已经应用于其他清洁航空项目,”Ascione 表示,“LRI 工艺特别适用于复合材料结构较厚的机翼、水平尾翼和垂直尾翼。”
清洁航空HERWINGT 项目将继续开发生产加固机翼壁板的 LRI 工艺 ,其中将研究树脂的不同配方,以提高玻璃化转变温度和雷击防护方面的性能。
OWB 开发的零件对零件装配技术已被证明具有潜力,并将在即将开展的国家研究项目中得到进一步发展。
2022年04年24日
2022年04年20日
2019年12年07日
2019年12年13日
2023年03年18日
2019年12年11日
2019年12年12日
2019年10年05日
2022年04年12日
2022年05年03日
评论 (0)