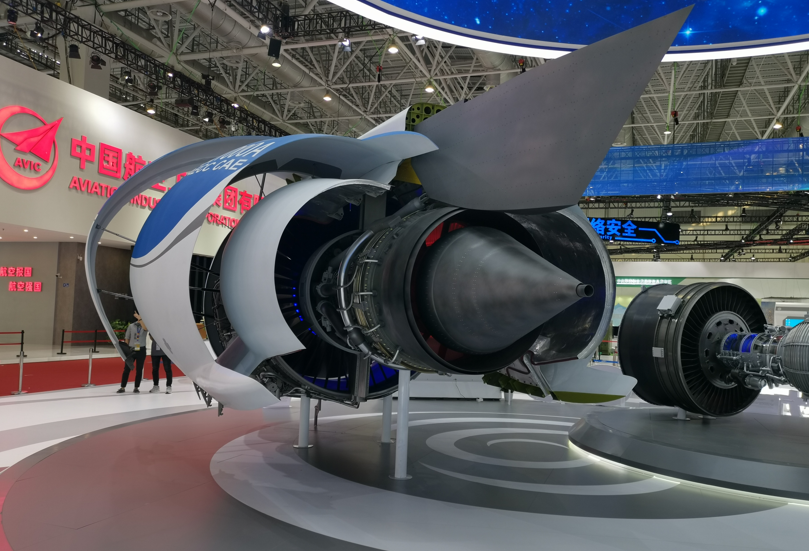
中国航空发动机集团简介、直属单位与主营业务
2022年04年24日
CompositesWorld 2025-04-18
提升性能并制造更轻、更坚固的部件一直是航空航天业发展的驱动力,促使制造商不断突破创新极限。这包括设计用于在碳纤维增强聚合物 (CFRP) 复合材料(包括热固性材料或热塑性材料)上钻铆钉孔的模具解决方案,用于机身、扰流板、机翼蒙皮和其他重要部件。
全球刀具公司肯纳金属(美国宾夕法尼亚州匹兹堡)表示,他们深谙复杂铆钉孔钻孔的复杂性,尤其是在加工多层堆叠板时。由于碳纤维增强塑料(CFRP)显著的轻量化优势,全球对碳纤维增强塑料(CFRP)的需求不断增长,加工过程中也面临一些挑战,例如频繁的换刀和设置。肯纳金属正在不断开发性能更佳的切削刀具系统,以克服这些挑战并满足行业需求。
在复合材料中钻铆钉孔的挑战
铆钉孔通常在CFRP或CFRP混合材料叠层(例如铝或钛)上进行。CFRP的加工极具挑战性,因为它们具有磨蚀性和各向异性;材料的强度和刚度会根据纤维方向和复合材料的分层方式而变化。如果操作不当,在这些材料上钻孔通常会导致分层、纤维拉脱,甚至孔错位。因此,至关重要的是要控制切屑并保持严格的公差,避免纤维损伤,并最大限度地减少毛刺形成,以保持工件的完整性。
有几种方法可以确保用户获得最佳的复合材料钻孔效果,包括以较小的增量去除材料、使用适当的工具和进给速度以及优化钻孔周期以确保孔的清洁。
“为了应对复合材料加工的挑战,关键在于采用能够提高精度并保持工件质量的策略,”肯纳金属公司CFRP和航空航天装配及未来解决方案工程技术项目经理Steve Gray说道。“可以考虑使用专用刀具,调整加工参数并优化工艺,以获得最佳效果。”
堆叠层压板加工的一个关键问题是保持锋利的切削刃,从而减少加工所需的力,并最大程度地降低毛刺形成和分层的风险。此外,还要注意刀具的磨损,因为磨损会导致过度摩擦并产生更多热量,从而增加分层和纤维拉脱的风险。在加工多材料堆叠层时,使用金刚石涂层或聚晶金刚石 (PCD) 钻头可以提高切削性能和刀具寿命,从而更容易保持严格的公差。
另一种可能的辅助方法是使用啄钻循环(也称为啄钻或啄铣)。该技术采用多次浅走刀,而非一次深走刀,是去除切屑并保持CFRP/金属叠层内部低温的有效方法。它可以防止孔内积聚金属切屑,避免切屑在排出时腐蚀CFRP。它还能防止刀具过热,避免树脂达到其玻璃化转变温度,从而避免损坏复合材料工件。
事实上,如上所述,热量积聚是导致零件损坏的主要因素,同时也会缩短切削刀具的使用寿命。值得注意的是,热塑性复合材料不易分层,但在钻孔过程中更容易受热量积聚和变形的影响。与此同时,热固性复合材料具有出色的热稳定性,在高温下不会熔化,但钻孔过程中产生的热量仍然会导致热降解并影响复合材料的机械性能。CFRP-钛合金混合复合材料需要同时处理这两种材料的技术,这带来了进一步的问题。
采用冷却液策略是控制温度的另一种选择。例如,在刀具切削刃上提供微量润滑 (MQL) 可以减少摩擦和热量积聚。
打造生态友好型环境的可持续解决方案
除了提高复合材料的切削效率外,切削刀具供应商还将可持续性作为首要任务,即寻找能够最大程度减少浪费和降低能耗的解决方案。微量润滑 (MQL) 技术是减少浪费的理想选择——通过在钻孔时将一定量的润滑剂直接施加到铆钉孔的切削区域,可以显著减少冷却液的用量。使用液态二氧化碳进行低温冷却是另一种降低刀具切削刃热量的有效方法。该技术使刀具保持极低的温度,有助于减少刀具磨损并更长时间地保持切削刃。
肯纳金属钻削和螺纹刀具全球产品经理 Georg Roth 表示:“客户经常联系我们,询问如何减少碳足迹。这涉及方方面面,从延长刀具寿命、降低硬质合金消耗到使用可回收包装材料。”
除了使用刃口刀片来避免浪费或使用模块化刀柄系统外,修复和重磨服务还旨在修复现有切削刀具,延长其使用寿命。这有助于减少材料使用,从而实现可持续发展,并降低单孔成本。
改进设计和性能
随着钻孔工具和技术的不断进步,CFRP 和热塑性塑料等材料的整合为肯纳金属公司的铆钉孔钻孔分层材料堆叠技术带来了重大创新。
例如,模块化钻头具有高刚性,可用于多种材料。超高抛光排屑槽可实现高效排屑,并且完全防止切屑流入接口并与工件接触。
SPF 型整体硬质合金钻头采用针对特定材料的设计,适用于加工复合材料和复合材料叠层。多层化学气相沉积 (CVD) 金刚石涂层可延长刀具寿命并提高耐磨性。90° 钻尖角设计提高了刀具的定心能力,并最大限度地减少了分层。
双角钻 (DAL) 适用于 CFRP-金属叠层钻孔作业。双角钻尖设计提供最佳定心能力,并最大程度减少从叠层金属侧钻出时的毛刺。DAL 钻适用于所有叠层组合:CFRP-钛-铝 (CFRP-Ti-Al),以及 CFRP-Ti、CFRP-Al 和直钛或直铝。即使使用微量润滑 (MQL),高度抛光的容屑槽也能确保最佳排屑效果。
正确的钻尖几何形状对于铆钉孔钻孔也至关重要,因为它可以确保准确的孔径和对齐,有效地减少热量并促进有效的切屑去除 - 最终增强飞机的结构完整性。
HiPACS钻孔和锪孔工具是另一款高精度系统,在航空航天紧固件孔应用中可实现 1° 的锪孔角度公差。HiPACS 设计用于夹紧在标准液压卡盘中,由三个标准组件组成:一个内置高精度锪孔刀片座的变径套、一个 PCD 锪孔刀片,以及具有 SPF 和 DAL 尖头几何形状的整体硬质合金或 PCD 钻头。这款易于组装的系统可在一次操作中完成钻孔和倒角。每个组件都可以独立更换,因此只需更换磨损的部件,其他部件即可继续使用。
HiPACS 精密刀具系统刀片位于排屑槽内,可实现最佳的过渡半径/倒角形状,避免孔与沉头孔之间出现台阶。此外,该系统的灵活性可减少传统一体式刀具的库存。直柄设计可在 10 毫米以内调节高度。该精密系统提供足够的间隙,使钻头能够保持 3-5 微米的跳动量。
在实际应用中,一家一级航空航天供应商希望降低其整体式组件的成本和复杂性。肯纳金属公司介入,用该公司的 HiPACS 系统替换了现有的整体式刀具组件,从而实现了最低的单孔成本,并显著减少了单项成本。
飞行员可以提供帮助
铆钉头不得超出飞机蒙皮,因为这会产生湍流和阻力。相反,可以通过沉头加工来实现平齐表面,使铆钉头与表面齐平。由于机械设备难以接近,沉头加工操作通常需要手动完成。为了解决这一难题,KenShape MaPACS 和MaxPAC S 导向 PCD 沉头钻专为手动沉头应用而设计,方便作。微动装置可实现精确的深度控制,使沉头钻在加工过程中保持稳定的质量。
铆钉孔钻孔的未来
铆钉孔钻孔是航空航天制造中的关键工序,而复合材料的转型正在推动切削刀具技术的进步。肯纳金属公司以此为契机,看到了复合材料孔加工的新方向。例如,正在开发传感器,用于在钻孔过程中进行引导、监控和调整,以防止刀具磨损和材料损坏。这些传感器可以实时进行,不仅可以优化孔加工工艺,还可以提高效率。
例如,肯纳金属公司最近与一位客户合作开展“单向装配”项目,该项目涉及开发基于传感器的技术,旨在简化飞机装配中的堆叠钻孔。通过使用传感器确保钻孔符合规格,可以省去清洁、拆卸和检查的环节,从而节省大量飞机部件的组装时间和成本。
航空航天业对更高性能和更轻部件的追求推动了切削刀具的创新,并且随着对 CFRP 的需求不断增长,这种趋势还将继续。
2022年04年24日
2019年12年07日
2022年04年20日
2019年12年13日
2023年03年18日
2019年12年11日
2019年12年12日
2019年10年05日
2022年04年12日
2022年05年03日
评论 (0)