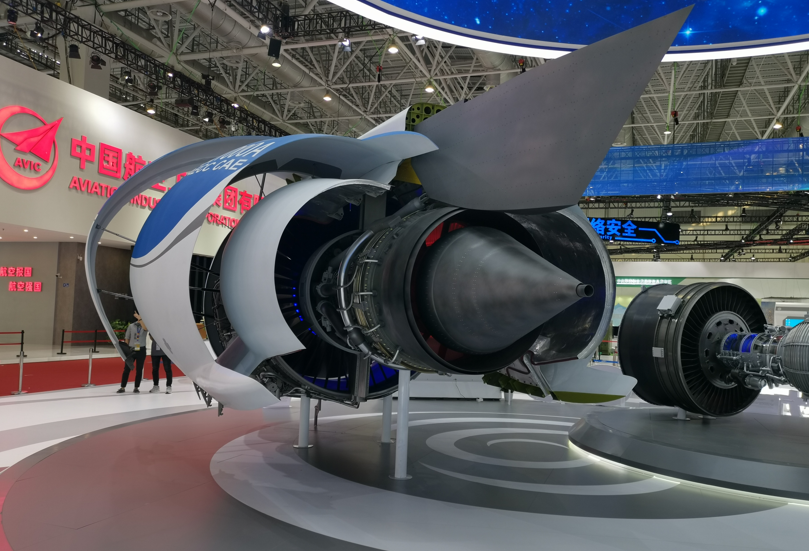
中国航空发动机集团简介、直属单位与主营业务
2022年04年24日
CompositesWorld 2025-03-19
2019 年, GKN AEROSPACE(英国布里斯托尔)技术总监 Craig Carr 与McLaren Automotive (英国沃金)之间的一次对话引发了英国最雄心勃勃的跨行业复合材料制造计划之一。讨论围绕一个引人注目的观察:McLaren 位于谢菲尔德的复合材料技术中心 (MCTC) 正在开发高度自动化的制造工艺,虽然按照汽车标准被认为是“低速率”,但在复合材料领域却代表了高速率生产。
这一认识引发了一个引人注目的问题:航空航天和汽车行业能否相互学习,将复合材料制造加速到新的水平?这一初步对话最终演变成 ASCEND(航空航天和汽车供应链支持开发)计划——这是英国复合材料行业为提高高生产率、工业 4.0和可持续复合材料制造而开展的一项重大合作。GKN AEROSPACE 从其位于布里斯托尔的全球技术中心 (GTC) 领导了该计划的技术方面,而 Axillium Research(英国伦敦)则提供了管理专业知识,将来自英国复合材料供应链的 15 个合作伙伴聚集在一起。
该计划于 2021 年初启动,为期 4 年,资金基础雄厚,达 3960 万英镑——其中 1960 万英镑由政府通过 Innovate UK 和航空航天技术研究所提供的支持,2000 万英镑则由行业合作伙伴提供。到 2025 年 3 月该计划结束时,已成功完成 17 个工作包,并在 42 个独立项目中达到技术就绪水平 (TRL) 6,展示了复合材料领域的重大技术进步。
GKN 公司的 Carr 从航空航天公司的角度回顾了该项目的影响。“ASCEND 是我们确定的技术开发机会的重要加速器。它显著提高了我们的复合材料制造能力。此次合作展示了航空航天和汽车之间的技术协同效应,这是我们在参与该项目之前从未完全预料到的。”
迈凯伦推动了该项目的汽车方面,旨在提高其公路车的复合材料精度和性能。MCTC 工厂总监 Joseph Elford 介绍了这家跑车制造商的成果:“MCTC 与 ASCEND 的合作旨在将传统上只能在小批量情况下实现的复杂设计转变为大批量、可扩展的生产方法。我们专注于弥合航空航天和汽车行业之间的鸿沟,采用成熟的航空航天技术(如胶带沉积)并使其适应汽车速度。这使我们能够优化光纤架构和拓扑,同时保持公路车生产的高吞吐量要求。与航空航天部门的知识交流非常宝贵,挑战了我们的方法并带来了自动化和材料科学方面的创新,使这两个行业都受益。”
ASCEND 联盟由 Axillium Research 精心策划,旨在确定和整合互补能力。每个英国合作伙伴都带来了独特的专业知识:Assyst Bullmer(韦克菲尔德)和 Loop Technology(多切郡)专注于自动化系统;Cygnet Texkimp(柴郡)和Sigmatex(柴郡)专注于材料加工;HEXCEL COMPOSITES(剑桥)、Syensqo Composites(前身为 Solvay,希纳)和Hive Composites(莱斯特郡)专注于先进材料开发;LMAT(布里斯托尔)和 FAR-UK(诺丁汉)专注于工具和制造工艺;Des Composites(谢菲尔德)专注于设计、测试和模拟;RAFINEX(伦敦)专注于优化软件;Airborne(兰伯恩)专注于自动化制造单元;国家复合材料中心(NCC,布里斯托尔)提供研究和可持续性框架开发。
该计划的结构是通过大量的研讨会和行业咨询而制定的,涵盖五个关键主题:轻量化设计工具、未来材料系统、速率自动化、电气化和多功能能力以及集成混合结构。
Axillium 董事长 Will Searle 表示:“通过将汽车行业的前期数字和虚拟工程方法与航空航天行业的严格认证协议相结合,我们为高速复合材料制造建立了新的范式。”“该计划表明,TRL 可以在不同行业采用不同的方法——航空航天 TRL 6 代表关键的投资门槛,而汽车开发可以通过多个设计周期快速迭代。这种交叉融合使我们能够开发行业中立的制造能力,其规模可以从 3 英尺的无人机组件扩展到 3 米的飞机结构。我们的虚拟技术审查会议和集成研讨会还营造了一种环境,即使在封锁限制期间,小型专业研发团队也可以有效协作,从而在基于物理的数字孪生和材料系统优化等领域取得突破性进展,以实现高速自动化。”
ASCEND 合作伙伴开发了多种材料技术和加工创新。
为了快速提高复合材料的质量,Hexcel 开发了 HexPly M51,这是一种快速固化预浸料系统,能够在 40 分钟内完全固化,无需后固化。经过 ASCEND 项目中的大量试验验证,HexPly M51 表现出与传统航空级材料相当的机械性能,同时与汽车生产速度相匹配。
HEXCEL COMPOSITES 项目经理 Lee Allgood 解释道:“我们的成功取决于集成复杂的加工模型——将动力学热分析与粘度分析相结合——这对于理解材料流动和防止空隙形成至关重要。”“这项开发利用了我们在配方化学方面的专业知识,创造了一个强大的预浸料系统,该系统既能进行高压釜加工,也能进行压机加工,同时实现热负荷加工效率。
Allgood 补充道:“我们通过制造具有复杂几何形状的零件和进行各种规模的自动化试验,验证了该材料的多功能性和高速加工性,这些试验范围从 6.35 毫米的自动纤维铺放 [AFP] 到 300 毫米宽的胶带铺设 [ATL],以及与 Airborne 合作进行的自动拾取和放置试验。”“在项目中,我们还与 LMAT 合作实施了数字孪生解决方案,使用有限元分析 [FEA] 仿真模型来实现最佳材料使用。最终产品不仅符合 HexPly M21 和 HexPly 8552 等航空航天标准的机械性能,而且在高温下将总固化周期缩短至 40 分钟,代表了加工效率的显著提高。”继该项目的开发之后,HexPly M51 系统现在提供单向 (UD) HexTow IM5-24K 和 IM9-24K 碳纤维以及玻璃编织和碳 PrimeTex(展开丝束产品)。
Syensqo 通过其 Cycom EP2750 快速固化技术平台为 ASCEND 的材料进步做出了贡献,这是实现汽车级生产速度同时保持航空航天质量标准的关键一步。Syensqo 航空航天和国防产品开发负责人 Luca Restuccia 博士表示,该材料系统将连续纤维预浸料功能与复杂的工艺控制相结合,使复杂的几何形状能够在 30 分钟内制造完成,这比传统的航空航天复合材料加工时间有了显著的改善。
Restuccia 表示:“与传统的航空复合材料工艺相比,Cycom EP2750 将生产时间缩短了 10 到 20 倍。该材料与双隔膜成型和弹簧框架压机制造等加工技术的兼容性使我们能够实现这些改进。通过将更快的加工与热压缩成型技术相结合,我们能够降低每个部件的成本,特别是对于较小的部件。这使得复合材料真正具有与传统机加工铝的竞争力,同时保持了航空航天应用的高性能要求。该系统在主要和次要结构中的多功能性,加上其增强的缺口压缩性能,使其非常适合高速率商用飞机项目以及军事和空中机动平台。”
Sigmatex 专注于为 McLaren 的高速率沉积技术开发专用胶带,以解决传统胶带卷轴容量有限而导致频繁停产的问题。该公司的研究带来了新的卷绕格式,可将停机时间减少三分之一,同时解决在汽车生产速度下保持航空级质量的复杂挑战。
“在开发高性能、高度对齐的碳纤维带时,我们遇到了一个根本性的挑战:密集的纤维排列提供了出色的机械性能,但也阻碍了树脂的渗透,”Sigmatex 首席纺织品开发工程师 Bryony Pigram 解释道。“我们的研究使我们优化了碳纤维上浆和 UD 结构,以实现与传统无卷曲织物 [NCF] 和机织织物相当的灌注速率,同时保持结构完整性。这种优化与我们的自动化质量监控系统相结合,使我们能够以汽车生产速度满足航空级规格。数字护照和实时质量验证的集成也改变了我们验证材料性能的方式,从手动检查转变为数据驱动的质量保证,可以跟上高产量制造需求。”
FAR-UK 的贡献集中在开发复合材料结构的迭代优化流程,将环境分析与先进的制造技术相结合。该公司的工作将材料选择、拓扑优化和环境影响评估结合到一个有凝聚力的框架中,以实现更可持续的制造能力。ASCEND 的一项关键创新是 FAR-UK 的协作机器人 (cobot) 粘合系统,该系统具有激光扫描功能和边缘检测功能,可在复杂几何形状上精确涂抹粘合剂。
FAR-UK 可持续发展工程师 Helena Job O'Connell 表示:“我们的流程与众不同之处在于计算设计与物理制造能力的无缝集成。我们开发了一个复杂的 FEA 分析框架,与 RAFINEX 软件协同工作进行拓扑优化,使我们能够根据特定的负载条件精确确定最佳粘合路径。我们的协作机器人将这种理论优化转化为物理现实——它们配备了激光扫描和边缘检测功能,可实现自动偏移分配,这意味着我们可以在复杂的几何形状上保持均匀的粘合剂应用。”
FAR-UK 在其汽车脚部工具项目中展示了这项技术,其团队首先通过计算优化了扭转和纵向载荷的粘合剂放置,通过 FEA 进行了验证,然后实现了可控焊缝厚度的精确无夹具粘合。
Cygnet Texkimp 在该项目内开发了三个系统:一个自动纤维缠绕单元,一个多辊堆叠机和一个热塑性预浸料机,用于为自动缠绕单元输送材料。
目标是什么?与传统的复合材料处理技术相比,Multi Roll Stack 的 S 型缠绕配置可将能耗降低 50%,同时在整个制造过程中保持恒定的温度。事实证明,这一进步对于生产适用于 5 型氢储罐的材料至关重要,而 5 型氢储罐是该计划更广泛的可持续发展举措的重点。
“Multi Roll Stack 的 S-wrap 结构代表了预浸料加工的根本性转变,实现了 10 米/分钟的生产速度,涂层重量为 112 克/平方米——是传统航空级材料生产速度的两倍,”Cygnet Texkimp 董事总经理 Luke Vardy 详细介绍道。“通过将多个浸渍辊垂直集成到一个压实模块中,我们消除了在线预浸料技术中常见的加热/冷却循环,同时通过速度控制的感应电机实现了精确的张力控制。这种配置对于 5 型氢气罐制造尤为重要,其中一致的树脂分布和纤维取向对于在极端压力下容纳动力学直径为 2.89 Ångström 的氢分子至关重要。该系统在加工过程中自动操纵织物编织的能力可优化悬垂特性和层间剪切强度,这也是高性能纤维缠绕复合材料在高达 1,000 bar 的压力下运行的关键特性。”
LMAT 专注于通过创新的工具解决方案解决装配难题。因此,其自加热工具系统可确保复合材料固化过程中温度分布均匀,同时无需机械辅助即可脱模。零腔囊和精确监控系统的集成进一步提高了 ASCEND 的工具技术水平,在制造迈凯伦的一款后扰流板时得到了显著的体现。LMAT 的技术总监 Tomasz Garstka 解释说:“我们的电阻加热技术通过优化直接层压到模具结构中的电气元件间距,实现了 ±4°C 以内的热均匀性。结合我们的零腔囊系统(可为脱模提供精确的 2 毫米组件高度)和我们的基于热的监控系统(能够检测碳纤维层压板中的流动前沿,这是传统成像技术无法实现的),我们创造了一个全面的解决方案,彻底改变了我们制造复合材料的方式。”
Hive Composites 开发的新型粘合工艺为先进的热管理提供了补充。该公司的董事 Peter Hansen 表示,在粘合部件本身内嵌入加热元件优化了大型复合结构的组装方式。开发的工艺在层压结构的粘合线上集成了一个导电层,从而能够在粘合剂界面处施加电流进行局部加热。通过将这些加热元件嵌入粘合部件本身,Hive 可以只加热粘合区域,而不需要大型烤箱来加热整个组件。
“我们的测试表明,与传统的全厚度加热方法相比,直接加热粘合剂界面可以提高粘合强度,”Hansen 说道。“该系统还可以在组装过程中实现精确的温度控制,使用更高的电流可以软化粘合剂,以便在需要时控制组件分离。这种配置允许在固化过程中同时进行修整和钻孔等操作,同时保持粘合区域的机械完整性。与传统的基于烤箱的粘合技术相比,直接界面加热方法已显示出显著的能耗降低。”
为了补充 LMAT 的自加热模具方法,Hive Composites 开发了一种新型模具系统,该系统将碳纳米管 (CNT) 基材料嵌入 CFRP 和 GFRP 模具中作为加热元件。与高压釜固化相比,该系统显著缩短了固化时间,并将能源需求降低了 90%,从而有可能消除对烤箱或高压釜的需求。还展示了工具面的热映射,精度为 ±2°C。
ASCEND 开发了各种自动化解决方案,包括从材料处理到过程监控的新方法。
在位于布里斯托尔的 GKN AEROSPACE 的 GTC,自动化树脂传递模塑 (RTM) 单元展示了 ASCEND 在自动化预成型、智能过程监控和优化材料处理方面的进步。
“通过 ASCEND,我们开发了一个集成制造生态系统,改变了我们生产复合材料结构的方式,”GKN 首席复合材料研究工程师 Tony Lloyd 解释道。“我们的自动化 RTM 单元将定制注塑设备与智能工具和感应加热相结合,所有这些都通过数字孪生框架进行协调。这使我们能够以汽车生产速度实现航空级质量。”
据 Lloyd 介绍,GKN 的突破在于该公司如何将热固性材料的快速压制成型与自动化处理相结合,从而能够在 30 分钟的周期内完成组件生产,完全省去了后处理步骤。“该单元的闭环过程控制由我们内部的缺陷快速识别系统支持,可确保始终如一的质量,而我们的自动成型技术源自汽车行业的见解,优化了我们处理先进材料的方式,”Lloyd 说道。
他补充道:“通过优化材料嵌套和节能感应加热,将这些功能与我们对可持续性的关注结合起来,我们不仅在改进现有流程,而且还在为高速复合材料制造建立新的基准,这对于城市空中交通 [UAM] 和下一代单通道飞机市场都至关重要。”
Airborne 对 GKN AEROSPACE 自动化 RTM 系统的贡献主要集中在其自动化铺层 (APP) 技术上,该系统旨在最大限度地提高复合材料部件的设计自由度,同时确保高速生产能力。
“我们 APP 系统的关键创新在于它能够从根本上改变我们自动化复合材料制造的方式,”Airborne UK 董事总经理 Joe Summers 解释道。“与仅限于胶带格式的传统 AFP 或 ATL 系统不同,我们的技术几乎可以处理任何材料格式——从干纤维和热塑性 UD 胶带到纺织品、薄膜,甚至夹层板的金属层片材。该系统的智能是围绕基于视觉的闭环控制架构构建的,该架构在连接到末端执行器时扫描每一层,将其实际位置与预期坐标进行比较,以实现实时轨迹调整。这种自适应定位对于实现航空级精度至关重要。
“真正让 APP 与众不同的是我们的自动化编程方法,”Summers 继续说道。“传统的机器人需要为每个新部件或材料进行大量的手动编程,但我们的算法可以在无需人工干预的情况下处理数千种不同的层形状。该软件考虑了材料的柔韧性特性,以优化夹持力分布和拾取策略,防止吸力点之间下垂等问题。它甚至考虑到了特定于材料的挑战——例如,在处理粘性预浸料时,我们的传感器可以检测未切割的纤维并自动暂停操作以进行操作员干预。”
该系统的智能延伸到质量控制和工艺优化。在放置之前,每层板都会经过检查,而 Airborne 的软件会不断从这些数据中学习。Summers 指出,该团队正在开发系统可以识别模式(例如,从切割机上始终准确的拾取)并动态调整检查频率以优化产量的功能。“缓冲系统增加了另一层复杂性,”Summers 说,“可以实现无序嵌套,从而显着减少材料浪费,同时保持生产流程。展望未来,我们正在实施‘针对 X 进行优化’的场景,制造商可以优先考虑不同的参数(无论是最大产量、最小浪费还是最低二氧化碳排放量),系统将实时自主调整其处理策略。这种级别的智能自动化对于使先进复合材料制造真正可扩展到高速率生产环境至关重要。”
Airborne 的 APP 技术集成了 Assyst Bullmer 的切割台技术,该技术可实现干纤维复合材料部件的自动沉积、剖析、预成型、修整和检查,以实现高速 RTM 加工。Assyst Bullmer 的切割解决方案通过针对航空航天应用的专有软件开发得到增强,在 CNC 切割机和机器人末端执行器之间建立了直接通信连接。
Assyst Bullmer 的总监 Martin Sofranko 解释道:“我们开发了算法,可以自动分析几何数据、优化吸盘定位并管理材料处理,而无需操作员干预。该软件系统通过材料缺陷的数字映射整合了故障映射功能,然后将其无缝集成到我们的嵌套算法中,以实现自动缺陷避免。我们还设计了专门的 DXF 过滤机制,可以将复杂的几何数据从数千条线减少到仅 12 条基本命令,从而显著提高处理效率。切割技术本身采用了特定应用的工具 - 从用于薄膜夹层材料的拖刀到用于干材料的驱动 10 面“披萨轮”刀片 - 具有智能过冲管理,可在编织材料中清洁释放纤维。”
Sofranko 指出,与手动操作相比,该系统的全面集成使能源效率提高了 60-80%,同时实现了复合材料制造中以前无法实现的混合订单生产动态。
ASCEND 项目内的数字系统开发从根本上重塑了复合材料部件的设计、制造和验证方式。
RAFINEX 成为该领域的主要创新者,开发了基于有限元物理的拓扑优化算法,可以分析超出理想化数字模型的结构。
RAFINEX 首席执行官 André Wilmes 强调:“我们的突破在于通过结合各向异性和多材料优化技术的随机有限元方法超越传统的各向同性假设。”“这种方法彻底改变了我们处理复合材料结构中现实世界变化的方式,使我们能够处理前所未有的海量数据——直接求解器优化中高达 2TB 的数据。通过将材料约束和操作条件集成到我们基于物理的拓扑算法中,我们从根本上改变了航空航天、汽车和更广泛的工业应用的设计优化格局。”
Des Composites 贡献了重要的模拟专业知识,特别是在高温预成型过程中对纤维的表征方面。该公司开发的自动化材料卡生成系统减少了对分析师专业知识的依赖,从而创建了更可控、更快捷的数据处理流程。Des Composites 还开发了一个内部设施,其中配有专用设备来测量关键的摩擦特性,因为这些特性会显著影响纤维在不同压力下的移动和层间动力学。
“通过最大限度地减少对个人分析师判断的依赖(通过我们的自动化材料卡生成系统),我们创建了一个更加一致和快速的过程,用于在产品开发从头到尾使用复合材料设计进行制造、装配测试以及工艺和性能模拟后,将物理行为转化为我们的数字孪生模拟,”Des Composites 项目经理 Lorenzo Gagliardi 表示。“这大大减少了复合材料制造中传统的反复试验阶段,同时保持了我们预测的高准确性。”
通过将 RAFINEX 仿真工具与 Des Composites 系统相结合,数字设计与物理制造之间的联系得到了显著加强。二者相结合后,可以准确预测制造结果,从而可以在生产开始前优化工艺参数。通过生产航空航天部件(包括翼尖结构的复杂几何形状),验证了模拟结果与实际结果之间的相关性。
Loop Technology 的 FibreEYE 解决方案的开发标志着数字制造集成领域的又一重大进步。该综合检测系统在两个关键领域运行:制造过程中的现场材料缺陷检测和铺层过程中的精确位置验证。通过对最佳照明和传感器配置的广泛研究,Loop Technology 创建了一个人工智能系统,该系统能够为材料卷生成数字护照,记录缺陷位置和特征。该公司的 3D 激光轮廓仪技术与分割算法相结合,能够实时监控铺层位置精度,这对于复杂的 3D 几何形状尤其重要。
Loop Technology 董事总经理 Alun Reece 解释道:“我们的技术将先进的成像技术与人工智能相结合,打造了一个全面的检测生态系统。通过将来自我们的 3D 激光轮廓仪的数据与精确的定位器信息关联起来,我们开发了一种分割算法,可以区分材料层并以最小的间隙重建复杂的 3D 布局。”
NCC 率先开发了复合材料制造环境评估的标准化框架。其可持续性成熟度水平 (SML) 框架超越了现有标准,为评估整个供应链的环境影响评估提供了通用语言。
SML 解决了与温室气体核算体系相一致的六个关键方面,包括完整性、相关性和透明度,使制造商能够系统地量化和改善其环境绩效。NCC 服务首席工程师 James Graham 解释说:“我们的框架超越了简化的全球变暖潜力指标,解决了复合材料制造数据敏感性的复杂性。我们实施了一个全面的评分系统,该系统评估多个参数的可持续性,同时保护专有流程。通过与 GKN AEROSPACE 的合作,我们展示了当直接供应链数据不可用时,如何将经验假设整合到生命周期评估中。我们开发的星爆式图表为决策者提供了可持续性绩效的多维视图,而不是将环境影响简化为单一指标。这种方法在热过程数据和能耗指标因其商业敏感性而需要谨慎处理的情况下被证明特别有价值。”
这些数字技术的整合为数据驱动制造创造了一个全面的生态系统。这种数字化转型超越了单个技术,创造了一个互联的制造环境,数据在设计、生产和质量控制系统之间无缝流动,代表着向工业 4.0 原则的重要转变。
ASCEND 项目的成果体现在两个旗舰样机上:GKN AEROSPACE 的叶片式翼尖和迈凯伦汽车的后地板组件。这些样机是整合联盟内部开发的多项技术创新的平台,展示了该项目在将航空航天精度与汽车生产率相结合方面的成功。
叶片式翼尖演示器代表了 GKN AEROSPACE 和 McLaren Automotive 之间的首次直接合作。GKN 根据单通道飞机的要求设计了该部件(包括蒙皮、翼梁和翼肋),同时融入了 McLaren 的制造原则。目标是雄心勃勃的:将节拍时间从 1 小时缩短到 30 分钟,同时保持航空航天质量标准。这是通过 McLaren 的专用 RTM 工艺实现的,该工艺最初是为其 Artura 插电式混合动力汽车的碳轻量架构 (MCLA) 开发的。
另一件展示品是迈凯伦的后地板组件,它展示了该公司的技术发展,特别是在减少废物方面。该组件制造工艺采用一种新颖的胶带沉积工艺,作为传统 AFP 的替代品而开发。这种复合胶带铺设的高速率工艺实现了近净成型生产,浪费最少,同时保持了受力蒙皮组件的结构要求,该组件在转弯载荷和制动力期间提供关键的稳定性。
“我们向基于胶带的方法的过渡使纤维结构得以增强,在方向和拓扑方面具有最佳保真度”,McLaren 的 Joseph Elford 指出。“通过创建净形状预制坯,我们有效地解决了定向连续纤维应用中常见的嵌套浪费问题,同时通过更精确的纤维排列实现了 5-10% 的刚度提升。这种方法与我们针对高速率生产优化的定制树脂化学相结合,使我们能够弥合复杂、传统小批量设计与可扩展制造方法之间的差距。关键是开发一种保持绝对均匀性和可重复性的工艺,消除了对大量工艺内传感和多个反馈回路的需求——本质上实现了‘一次成功’的方法,正在改变我们处理复合结构的方式。”
迈凯伦通过 ASCEND 开发的工具系统无需在零件之间进行清洁或维护,可通过机器人零件拆卸和即时工具重新装载实现连续生产——据说这种能力以前在复合材料制造中是无法实现的。两台演示机都受益于先进的工具创新,包括自加热形状记忆聚合物工具,这大大缩短了加工时间和成本。
ASCEND 总结称,该项目的影响远远超出了直接的技术成就,为跨部门合作建立了新的典范。例如,根据 Axillium 的 Will Searle 的说法,该项目已在英国成功创造了 2,000 多个技术岗位,建立了一支能够支持下一代复合材料制造技术的劳动力队伍。
值得注意的是,NCC 开发的 SML 框架的持久贡献代表了该行业的环境未来。这种衡量和传达整个供应链可持续性的标准化方法为制造商提供了实现净零目标的明确途径。该框架与 GKN AEROSPACE 运营的整合已经证明,通过过渡到非高压釜工艺,能源消耗有可能减少 80%,为可持续制造树立了新的标杆。
Carr 还强调了 ASCEND 如何改变了 GKN 未来飞机部件制造的方法:“该项目成功实现了每月 100 艘的生产率,使 GKN AEROSPACE 能够满足传统航空航天和新兴 UAM 市场日益增长的需求。汽车启发的自动化制造流程的集成为未来的生产设施创建了一个模板,有可能显著降低成本和环境影响。”
展望未来,Axillium 通过 ASCEND 开发和完善的结构化创新框架为未来的跨部门合作提供了蓝图。该计划在管理 15 个不同组织之间的复杂合作关系方面取得了成功,证明了如何超越传统行业界限以实现共同目标。这种合作模式由数字集成和标准化可持续性指标支持,为行业合作树立了新标准。
该计划的遗产可能最明显地体现在其对未来产品开发战略的影响上。航空航天和汽车合作伙伴现在都以更广阔的视角来看待设计和制造,吸取彼此领域中的经验教训。这种思想的相互影响,加上建立强大的供应链和熟练的劳动力,将继续为英国复合材料行业在未来几十年的持续增长和创新奠定基础。
2022年04年24日
2019年12年07日
2022年04年20日
2019年12年13日
2023年03年18日
2019年12年11日
2019年10年05日
2019年12年12日
2022年04年12日
2022年05年03日
评论 (0)