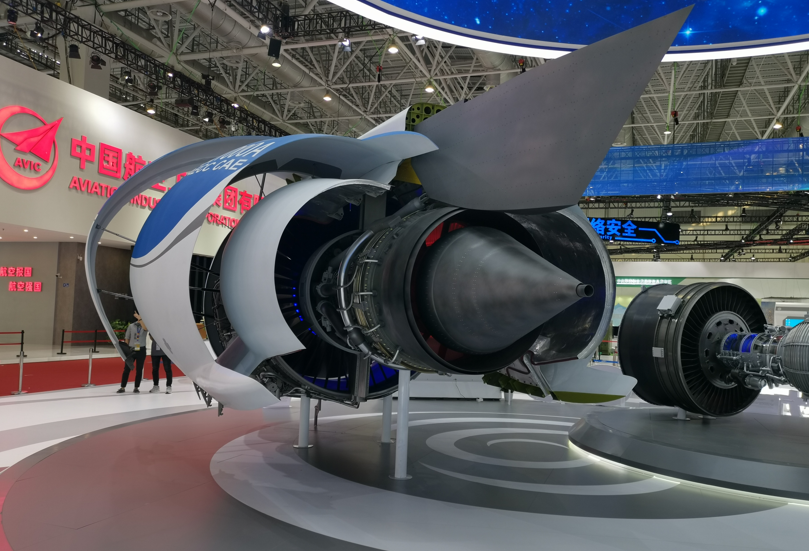
中国航空发动机集团简介、直属单位与主营业务
2022年04年24日
CompositesWorld 2024-05-10
DCeraTurb 项目研究团队由德国航空航天中心(DLR,科隆)内的多个研究所组成,正在探索如何使用陶瓷基复合材料(CMC) 来制造航空发动机的高压涡轮叶片。目标是减轻重量以及对冷却空气/昂贵冷却剂的需求,从而减少排放,实现净零航空。这些新型 CMC 入口导流叶片由跨学科团队开发、制造、涂有环境屏障涂层 (EBC) 并进行测试。
DLR 结构研究所 陶瓷复合材料和结构设计部门最近制造了三个 SiC/SiC 涡轮叶片。在 3DCeraTurb 项目期间,DLR 的液体硅渗透 (LSI) 制造工艺首次从平板调整为更复杂的几何形状。一个特殊的挑战是将干燥的织物层覆盖到石墨模具中以施加化学气相渗透(CVI)纤维涂层。另一个亮点是演示了圆柱形冷却孔可以集成到 CMC 叶片的后缘,而不会损坏材料。
随后在哥廷根 DLR 推进技术研究所进行了风洞测试。新型耐热入口导叶由 SiC/SiC CMC 制成,适用于齿轮涡轮风扇发动机。纤维增强陶瓷的密度较低,可以减轻这些部件的重量,从而减轻整个发动机的重量,从而提高推重比。此外,由于 CMC 具有耐高温特性,无需冷却液,但涡轮叶片可承受高达 1315°C 的温度。
DLR 的3DCeraTurb项目(2021-2024)专注于使用 SiC/SiC CMC 设计和制造涡轮叶片,目标是建立 CMC 组件设计、制造、EBC 涂层、风洞验证和损伤评估的工艺链。
高压涡轮进口导叶。新的涡轮轮廓是根据 DLR Perfect 项目现有 UHBR-GTF 发动机初步设计的发动机侧边界条件设计的。复杂的叶片几何形状是制造过程的主要挑战。将 CMC 制造技术从平面样品升级到 3D 组件是提高这些材料可用性的关键,这些材料在热气路径中具有更高的耐温性。
改进了 CMC 寿命预测。 制造过程信息和数据将被集成到多尺度仿真中,以考虑制造影响并改进 CMC 零件的整体建模和寿命预测。除了材料的微观结构之外,还可以使用相场方法在整个操作期间一致地考虑寿命限制的损伤萌生和损伤演化。来源数据系统将确保项目生成的数据的可追溯性和一致性,该系统是涵盖空气动力学、结构力学和可制造性各个方面和细节的自动化流程链的第一个组成部分。
风洞测试。为了分析和评估空气动力学性能,这些 CMC 叶片已在哥廷根 DLR 推进技术研究所 TRL 4 的直叶栅风洞中进行了测试。
2022年04年24日
2019年12年07日
2022年04年20日
2019年12年13日
2023年03年18日
2019年12年11日
2019年10年05日
2019年12年12日
2022年04年12日
2022年05年03日
评论 (0)