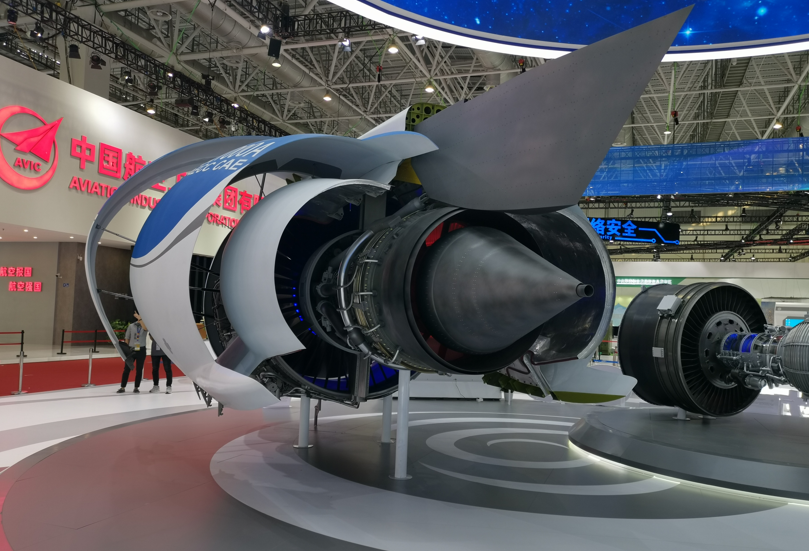
中国航空发动机集团简介、直属单位与主营业务
2022年04年24日
航空产业网 2025-04-22
在航空航天制造业领域,生产制造呈现出周期漫长、制品要求严苛、质量控制标准严格以及生产数量相对较少等显著特征。这些特性不仅对生产成本产生深远影响,更使其成为决定企业核心竞争力的关键因素。在此行业背景下,生产工艺优化成为企业突破发展瓶颈、实现突围的核心路径。通过对生产流程进行系统性改造,企业不仅能够直接降低制造成本,还能重塑供应链价值,在效率、质量、响应速度等多个维度实现全面提升与突破。值得强调的是,这种生产工艺的优化并非简单的技术改进,而是一场以成本动因分析为坚实基础、以精益思维为行动指南、以价值流动重构为最终目标的战略转型。其本质在于,在生产环节的微观层面,通过消除各类浪费、显著提升生产效率,从而释放出被传统生产模式所束缚的利润空间。
工艺优化的首要任务在于构建工序级的成本核算体系,以此将传统成本管控中如同“黑箱”般难以洞察的部分,拆解为可观测、可分析的作业单元。企业需对每个产品线的生产流程展开极为细致的成本分解工作,具体涵盖动因溯源、价值分类以及改善靶点定位等环节。
动因溯源就是要精准识别每个生产环节的成本驱动因素,像设备折旧、人工工时、能源消耗、物料损耗等,明确成本产生的具体作业点。
价值分类则是基于客户价值视角,将生产操作划分为增值操作(如机械加工、部件组装)与非增值操作(如物料等待、无效搬运、重复检验),增值操作直接赋予产品功能,非增值操作虽为生产所必需,但并不直接增加产品价值。
改善靶点定位则通过成本动因分析,锁定高成本、低效率的作业环节作为重点改善对象
这一系列过程要求企业组建跨部门的成本分析团队,融合财务、质量、生产、工艺等多维度数据,保障成本核算的精准性与全面性。当成本动因被清晰解码后,企业便能够以数据为导向,将资源聚焦于最具改善潜力的环节,有效避免因盲目投入而造成的效率损耗。
在成本动因分析的基础上,企业需引入精益生产(Lean Production)理念,系统性识别并消除生产过程中的八大浪费:
过度生产:生产超出客户需求的产品,导致库存积压与资金占用。
库存浪费:原材料、在制品、成品的过度储备,掩盖了生产中的效率问题。
等待浪费:设备、人员、物料的闲置,造成时间成本的无谓消耗。
运输浪费:物料在工序间的非必要移动,增加搬运成本与质量风险。
过度加工:超出客户需求的功能或质量标准,导致资源浪费。
动作浪费:员工的无效动作(如弯腰、转身、重复操作),降低劳动效率。
缺陷浪费:因质量问题导致的返工、报废、客户投诉,增加隐性成本。
技能浪费:员工未被充分调动的技能与知识,造成人力资本的闲置。
针对生产中的各类浪费,企业应采取三方面连贯举措加以改善。借助价值流图分析开展流程再造,优化生产流程逻辑、消除非增值环节;通过建立标准工时与标准操作流程(SOP)实现标准化作业,降低变异性与浪费;运用PDCA循环形成持续改进机制,营造全员参与的改善文化,以此实现生产效率与质量的稳步提升。
行业案例分享
在航空航天制造领域,高精度、高质量的零部件生产是确保飞行安全与性能的关键。2009 年,韩国航空航天工业公司(KAI)凭借卓越的技术实力与创新理念,成功获得英国空客公司青睐,成为 A350 机翼肋板的供应商。A350 机翼肋板作为大尺寸精密机加工零部件,对加工精度、质量把控以及生产流程的完整性都有着极为严苛的要求,其加工工序繁多,涵盖上料、机加工、去毛刺、磁粉探伤、尺寸检测、厚度检测、产品下线、运输仓储等关键环节。
面对如此复杂的生产需求,KAI公司并未遵循传统的生产方式,即依据生产设备布局安排生产与零部件周转。相反,公司大胆引入精益生产理念,构建起一条高度自动化、柔性化的 A350 机翼肋板柔性生产线。该生产线集成了自动上料系统、5 轴加工中心设备、毛刺设备、自动荧光检测、自动 CMM 检测、自动厚度检测以及自动物流传送等一系列先进系统设备,全面满足 A350 机翼肋板的所有生产工艺要求。
具体而言,A350 机翼肋板生产的柔性制造系统配置丰富,包含 7 台机床、60 个交换工作台、4 个设置站和 2 台轨道车。为实现生产流程的高效协同,KAI 公司采用单元化生产布局,将这些设备依据生产流程精心组合成 U 型单元。这一举措成效显著,零件周转距离从原本的 800 米大幅缩减至 50 米,极大地提高了生产效率,降低了物流成本与时间损耗。
在数控编程环节,KAI 公司创新性地嵌入“工艺校验模块”。该模块具备自动识别超差加工指令的功能,有效避免因编程错误导致的生产问题,使编程错误率从 9%大幅降低至 0.5%,从源头上保障了产品质量的稳定性。
针对生产过程中工装夹具更换环节存在费事费力这一瓶颈问题,KAI 公司研发出了磁性工装夹具。这一创新成果将模具更换时间从原本漫长的 4 小时压缩至 18 分钟,显著提升了生产线的灵活性与响应速度,使得生产能够更加快速地适应不同型号、不同规格产品的生产需求。
通过一系列创新举措的实施,KAI 公司的 A350 机翼肋板生产取得了显著成效。部件交付周期大大缩短,能够更快地响应客户需求;部件质量上乘,产品展现出卓越品质,从而赢得了客户的高度认可与信赖。
KAI 公司的这一成功案例,为航空制造企业提供了宝贵的借鉴经验。它充分展示了精益生产理念与先进技术融合的强大力量,通过创新生产布局、优化生产流程、提升设备性能,企业不仅能够实现生产效率的大幅提升,同时确保产品质量的稳定可靠,最终能够驱动供应链总体成本的优化。
我们的服务
捷一科技作为航空产业网研发运营主体,能为企业提供成本核算、成本驱动因素识别与价值分类、精益生产理念导入与浪费消除、流程再造及标准化作业、持续改进等全方位工艺优化服务,助力企业降低生产成本、重塑供应链价值、提升生产效率与质量,实现多维突破与核心竞争力增强。有意者请联系
订阅咨询与系统演示
全面、及时、准确地洞察行业趋势、热点和发展机遇,是抢占市场先机、建立行业深度认知的关键。欢迎联系我们查询更多项目信息,航空产业网将为您提供航空航天领域的一手信息,助您占领信息高地。
欢迎点击阅读原文注册或扫描下方二维码添加客服,免费试用“经度”系统。
2022年04年24日
2022年04年20日
2019年12年07日
2019年12年13日
2023年03年18日
2019年12年11日
2019年12年12日
2019年10年05日
2022年04年12日
2022年05年03日
评论 (0)