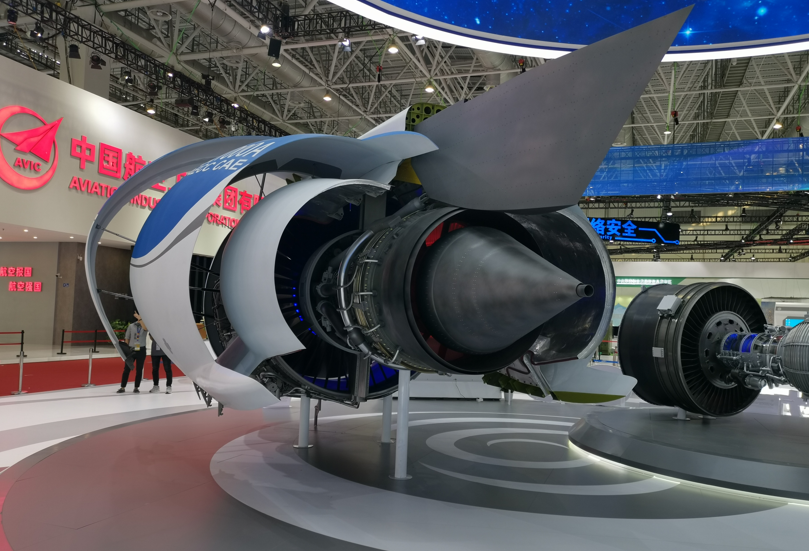
中国航空发动机集团简介、直属单位与主营业务
2022年04年24日
金属3D打印专家铂力特 2025-04-24
近日,陕西天回航天技术有限公司自主研发的85吨级火箭发动机“巧龙一号”(QL-1)顺利完成50秒试车。试验过程中,发动机起动平顺、关机迅速,全程运行高效稳定、状态完好,标志着我国航天动力技术实现又一重大突破。这一成果的取得,既凝聚了天回航天团队的不懈努力,还得益于铂力特的关键技术支持。铂力特为“巧龙一号”发动机深度定制并打印了包括涡轮泵、推力室、阀门等在内的20余项核心零部件,发动机上主要3D打印零件均由铂力特提供,为试车成功奠定了坚实基础。
在火箭发动机系统中,推力室和涡轮泵是保障其可靠运行的核心部件。针对“巧龙一号”发动机的不同零部件需求,铂力特从设计初期便深度参与,通过3D打印一体化成形技术,精准打造发动机推力室和涡轮等关键组件,使发动机的综合性能得到有效保证。
推力室作为火箭发动机的动力源泉,能将燃料燃烧产生的高温、高压燃气热能转化为动能,为火箭提供飞行推力。在“巧龙一号”发动机研制过程中,铂力特采用BLT-S800、BLT-S515、BLT-S1000、BLT-S450设备,分别实现推力室扩张段、发生器、推力室身部及氧进口等关键部件的一体化制造。传统工艺受加工方式限制,难以实现复杂流道结构制造,且需经过焊接、组装等多道工序,影响零件性能。3D打印技术凭借一体成形优势,能够精准构建复杂流道结构,优化推进剂的流动路径,显著提高燃烧效率并降低能量损耗,从而为发动机提供更强大的动力支持。
推力室扩张段(图片仅为示意) 涡轮泵是火箭发动机的“心脏”,通过涡轮驱动泵体,将推进剂加压输送至燃烧室,确保发动机燃料持续供应。在“巧龙一号”发动机研制中,铂力特为其打印了两级轮盘、涡轮导叶、燃料壳体、氧化剂壳体等多项零件,有效降低了零件制造成本,提升了生产效率。两级轮盘(图片仅为示意) 传统工艺需经过切削加工、电极设计、电火花加工等环节,制造周期长、成本高,且难以适应零件设计的快速迭代需求。3D打印技术通过整合工序实现一体成形,能够简化生产流程,加速零件研发进程。 以两级轮盘为例,零件尺寸为340mm×340mm×55mm,采用BLT-S450设备一体打印成形。在传统工艺下,该零件从材料采购到加工,单件研制成本高达20万元,制造周期最少需3个月;利用3D打印技术,单件成本降至5万元,制造时长缩短至45天。这不仅显著提高了生产效率,实现了零件快速制造,还为结构设计的高效迭代提供了技术保障。
铂力特与天回航天的携手合作,实现了火箭发动机关键零部件的高效、低成本制造,为发动机试车的圆满成功筑牢根基。不仅如此,此次合作还树立了3D打印技术与航空航天领域深度融合的新典范,拓宽了3D打印技术在航天领域的应用范畴,为航天制造领域工艺革新注入新动能。
2022年04年24日
2019年12年07日
2022年04年20日
2019年12年13日
2023年03年18日
2019年12年11日
2019年12年12日
2019年10年05日
2022年04年12日
2022年05年03日
评论 (0)