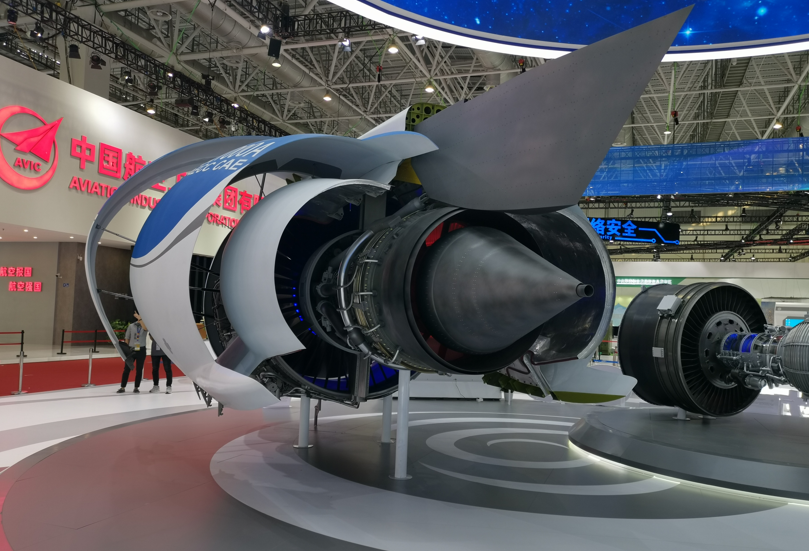
中国航空发动机集团简介、直属单位与主营业务
2022年04年24日
CompositesWorld 2025-02-07
航空航天业越来越多地使用复合材料来制造更轻、更坚固、更高效的现代飞机。复合材料的重量比金属材料轻 20%,强度比铝、钢和钛高,非常适合减轻大型结构和机身部件的重量。它们还为工程师提供了更大的设计灵活性,因为它们可以模制成传统材料无法实现的复杂形状。
对于制造商来说,缺点是这些材料难以加工,因为它们具有磨蚀性且容易碎裂。例如,碳纤维增强聚合物 (CFRP) 的磨蚀性极高,将带来诸多挑战,包括切削刀具快速磨损、切削质量下降、温度升高、振动和切削条件不稳定。与传统金属加工相比,标准硬质合金切削刀具在切削 CFRP 时可能只能维持其正常刀具寿命的 5%。
由于复合材料的特性千差万别,因此没有简单的公式可以克服这些挑战。不过,每个车间都可以应用一些关键的最佳实践和切割原则来应对这些动态并改善运营。
首先要了解的是,复合材料可以有各种各样的组成材料,这些材料通过基质或分层增强材料加入,这意味着它们可以具有各种各样的物理和化学特性。复合材料除了碳纤维外,还可能含有其他增强材料,如玻璃纤维、芳纶(凯夫拉)或其他纤维合成材料。还可以添加陶瓷或金属粉末以及各种添加剂,如二氧化硅或二氧化硅,以增强材料性能。
了解复合材料的组成及其在加工过程中的表现对于实现最佳机器设置至关重要。例如,切割由单层组成的单向 (UD) 材料可能会带来独特的挑战。当纤维沿同一方向排列时,它们不会为材料结构提供支撑,并且在加工操作过程中容易受到拉扯和磨损。车间需要从适当的角度和方向进行切割,在某些情况下,需要使用从材料的顶部和底部进行切割的压缩式工具。
复合材料的另一个挑战是它们通常与其他材料(如钛、铝或铜)以各种组合堆叠在一起。当一次性钻穿这些组合时,车间需要了解钻头将如何与每层材料相互作用。对于堆叠的碳纤维和铝,操作员可以在切割过程中保持相同的快速切割速度,但对于钛等较硬的材料,可能需要在钻孔操作期间调整每层的切割速度和进给率。
复合材料在加工过程中会产生大量有害粉尘。这不仅对呼吸健康有害,而且粉尘颗粒对机器电子设备和设备也极具破坏性。此外,大多数飞机制造商都不能让碎片滞留在飞机结构内,因此必须高效除尘。为了控制这些颗粒,请安装合适的筒式集尘器,并尽可能密封机床外壳。如果主轴正确封闭,一个简单的车间真空附件也可以满足要求。
由于复合材料具有极强的磨蚀性,高速钢甚至硬质合金切削刀具都可能很快失效。由于故障而频繁更换刀具会导致生产力下降,尤其是在加工大型结构部件(如翼盒)或钻数千个铆钉孔时。在这些应用中,投资聚晶金刚石 (PCD) 刀具非常值得,因为它们的使用寿命是标准切削刀具的 10-15 倍,可提高工艺安全性和表面质量。这些刀具可保持更长时间的锋利度,并在复合材料中提供更干净的切割,从而降低可能导致部件报废的磨损或故障风险。
金刚石刀具表面可能涂有金刚石涂层,采用化学气相沉积 (CVD) 工艺,或者采用烧结到硬质合金中的金刚石脉纹制成。脉纹切削刀具代表了复合材料加工的重大进步,使 PCD 能够放置在螺旋脉纹中,以获得更好的螺旋几何形状和切屑流动。这减少了切削力,特别是在钻头出口处。
优秀的切削刀具供应商将使用复合材料对 PCD 刀具进行大量测试,以提供关于性能和预期寿命的清晰数据,从而帮助实现更可预测的结果。他们还能够通过修复延长刀具的使用寿命,这是近年来有所改善的领域。以前,PCD 刀具可以重新打磨两到三次,而现在,某些刀具可以重新打磨多达 10 次。重新打磨的成本通常为新切削刀具成本的 20%,因此这大大提高了投资回报率。
加工工艺不高效会导致复合层压板分层,从而对部件的结构完整性和表面质量造成不利影响。为了避免这种层分离,必须使用能够最大限度减少材料抬升的切削刀具几何形状。例如,选择用于去除材料的铣刀,其螺旋角应较小(最多 10° 到 15°),这样铣削操作就不会将材料拉开。
此外,一旦刀具开始变钝,它就会立即开始挤压材料,而不是进行平滑切割,从而导致碎裂。为了避免这种情况,请选择能够保持更长时间锋利边缘的刀具,例如带有 PCD 刀尖的钻头,并且不要超出预期寿命的极限——当切削刀具开始失去锋利时,请更换它们。为了更长时间地保持锋利,可以使用策略来管理刀具磨损,例如在侧铣操作中将刀具定位在凹槽上进行进一步切割。这可以使刀具磨损更加均匀地分散,并延长刀具的使用寿命。
市面上有各种锋利的工具,它们专为提高复合材料的性能而设计。例如,压缩螺旋铣刀(如 Sandvik Coromant 的 CVD 涂层 CoroMill Plura)有助于减少修整时的分层和悬挂(未切割的纤维),而脉纹 PCD 立铣刀则非常适合正交切削,例如开槽、修整和开槽。对于钻孔,脉纹金刚石钻头通常配有特殊的边缘倒角、半径甚至经过修改的麻花钻头(类似于木工钻头),以防止在突破时分层或碎裂。
典型的机床操作员在切削过程中会倾听,如果发现任何异常,他们往往会降低切削速度和进给率。这也是一种常见的做法,旨在延长切削刀具的使用寿命。但在复合材料加工中,这种谨慎的加工方法往往会导致问题。复合材料加工的声音很难听清,进给率和切屑负荷(切削刃在每次旋转时产生的切屑宽度)过低会导致摩擦、颤动、分层和刀具过度磨损。
机械师还必须学会阅读切削刀具上的磨损模式并相应地调整刀具路径。如果铣刀磨损过度,操作员可能需要考虑在 Z 方向调整刀具,以使用更多的刀具来减少磨损并避免分层。对于钻孔,换用麻花钻可能会防止孔背面的分层。由于复合材料种类繁多,尝试不同类型的刀具和工艺参数,或与刀具供应商合作找到正确的几何形状通常是最好的方法。
切割复合材料,尤其是切割用于飞机地板和机舱隔板的夹层蜂窝材料,可能非常困难——大多数情况下,刀具只是将面板推开。这里的关键是保持积极性,保持 6,000-10,000 rpm 的切削参数和每齿 0.002-0.003 英寸范围内的高切屑负载。这也有助于通过将热量通过切屑传递到切削刀具来最大限度地减少材料中的热量积聚。这在使用热固性材料和热成型/热塑性材料时尤其重要,这样材料就不会粘附在刀具上。如果刀具的切屑负载小于 0.001 英寸,它们会很快被损坏。
在这里使用 PCD 或 CVD 工具将使操作能够保持所需的积极切割。例如,Sandvik Coromant 的 CoroDrill 863 具有 -O 几何形状,提供专为钻削复合材料而设计的 PCD 或 CVD 选项。优化的钻头具有独特配方的基体,可更好地粘附涂层,并具有高轴向前角以减少分层。PCD 纹理 CoroDrill 859V 针对 可能使用预浸料系统以及环氧树脂和双马来酰亚胺的 UD 材料进行了优化。双角度几何形状有助于减少要求苛刻的材料上的分层。
另一个考虑因素是冷却剂的使用。使用冷却剂控制热量通常不是一种选择,因为冷却剂可能会进入复合层压板并污染材料。为了降低热量,车间可以在切割区使用压缩空气或冷风枪,并配备足够大小的集尘系统,这是一种低成本的解决方案。
牢固而安全的刀架至关重要,可防止切削过程中的颤动,而颤动可能会毁掉对优质加工工具的投资。液压卡盘可最大限度地减少跳动和刀具拔出的可能性——这些事件可能会导致 40,000 美元的 CFRP 翼型报废。在较高的主轴速度下(任何超过 20,000 rpm 的速度),最好将刀架作为一个完整的组件进行平衡,并安装切削刀具和固定旋钮以保证刀架安全。
夹紧复合工件也很重要。如果工件的表面积足够大,可以产生足够的夹紧力,则真空夹具非常有用。在大多数情况下,夹具是最佳选择,尤其是对于复合工件常见的复杂 3D 形状。夹具的设计应避免任何不受支撑的切割区域,同时仍能牢固夹紧以防止部件移动和振动。
由于复合材料加工涉及如此多的变量,因此要找到正确的机器设置和正确的工艺可能是一项艰巨的任务。通过测试来验证新部件或新材料的工艺需要时间和资源,而许多车间都没有这些资源。但是,重要的是要记住,您并不是孤军奋战。与刀具供应商合作不仅可以获得刀具建议,还可以成为工程和支持的宝贵资源。除了刀具选择指导之外,他们还可以使用与您的车间相同类型的设备在测试设施中帮助进行刀具路径编程、模拟和加工新部件。像 Sandvik Coromant 这样的供应商甚至可以定制客户专用刀具以满足部件的需求。
复合材料是机械师面临的最具挑战性的材料之一。加工这些材料的过程尘土飞扬、艰巨而又磨蚀性强,对切削刀具要求很高。但只要正确组合切削刀具、切削策略以及内部团队和/或刀具供应商合作伙伴的专业知识,任何车间都可以更成功地生产航空航天复合材料。
2022年04年24日
2022年04年20日
2019年12年07日
2019年12年13日
2023年03年18日
2019年12年11日
2019年12年12日
2019年10年05日
2022年04年12日
2022年05年03日
评论 (0)